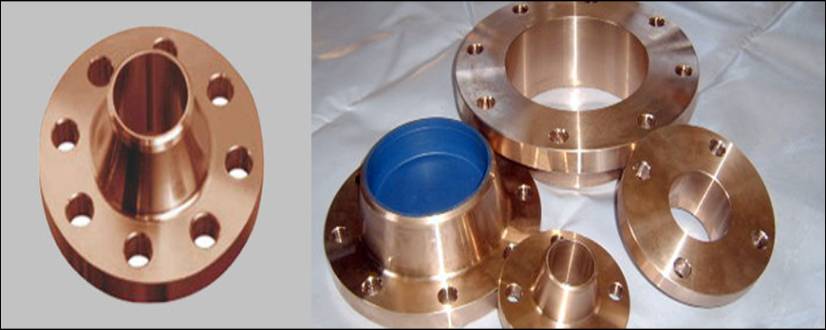
With excessive nickel content, this product is proof against chloride-brought about strain corrosion cracking. This product resists corrosion through dry chlorine and hydrogen chloride. Forging of this product is to be completed through managed procedures. Cu-Ni 70 / 30 Orifice Flanges is an expensive alloy in usage, and for this reason its use is restricted to those applications wherein it can't get replaced with inexpensive alternatives.It is a solid-answer binary alloy, and sothe ratio of copper to nickel on this metallic is nearly same to that discovered within the ore the steel is derived from. This metallic has notable resistance to hastily flowing brackish water or seawater.
Typical applications of this metallic are marine furniture and fasteners; valves and pumps; pump and propeller shafts. This metallic is in particular immune to hydrochloric and hydrofluoric acids whilst they're de-aerated. The spark unfastened nature of this metallic lends itself to excessive danger conditions within the explosives industry, rocketry and the pulp and paper industry. Copper Nickel WNR 2.9882 Blind Flanges possesses notable corrosion resistance to many lowering media. This metallic is frequently utilized in springs; electric and digital components; chemical processing equipment. This metallic is likewise utilized in Marine Engineering, Hydro-carbon Processing, and Chemical Processing. This metallic is likewise normally extra immune to assault through oxidizing media than better copper alloys.
This metallic famous notable weldability, and isn't always prone to SCC. This metallic is frequently discovered in marine applications together with seawater valves and pump shafts. This metallic additionally has properly mechanical properties from sub-0 temperatures as much as 549 Degree C.Copper Nickel UNS C71500 Spectacle Blind Flanges is without difficulty weldable, has properly resistance to non-oxidizing acids, and is likewise now no longer prone to chloride strain corrosion cracking. Cold working for this product can be completed the use of smooth die materials for higher finishing, due to the fact it could be annealed at 926 Degree C (1700 Degree F).