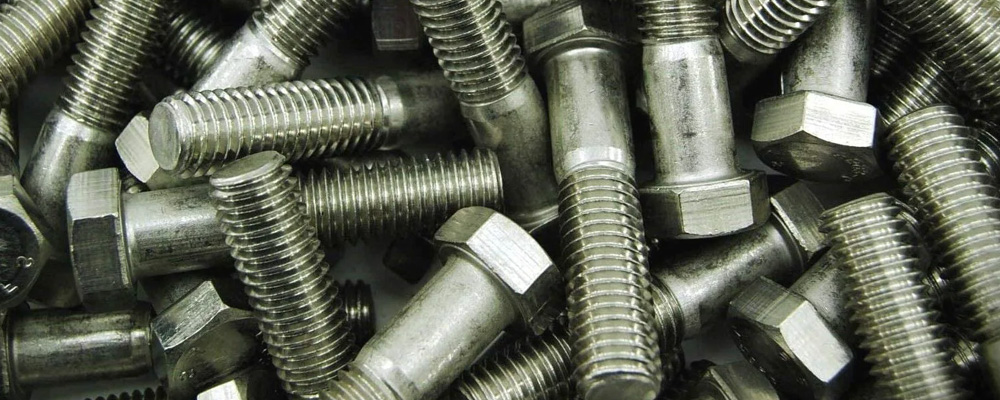
It is concluded that consequences of cooling and lubrication will be progressed via way of means of imparting excessive-pressure coolant. With increased coolant pressure in Stainless Steel UNS S31700 Bolts, penetration functionality of coolant in crucial zones (device-chip or device-paintings interfaces) turned into more advantageous. Therefore, to lessen such microstructural deformation, utilization of such lined gear turned into additionally really restricted. It is likewise pronounced that excessive-pressure coolant supplied minimal surface damages to the machined surface than traditional turning. Thus, slicing fluid application for Stainless Steel WNR 1.4449 Nuts seems positive over dry machining. However, application of a massive quantity of slicing fluids frequently seems destructive for each surroundings in addition to operator’s heath. Moreover, cost economic system turned into any other vital issue for choice of an appropriate slicing device, in purview of which tungsten carbide regarded because the excellent choice.
In the case of dry machining, immoderate slicing temperature is localized on the device-tip. Stainless Steel UNS S31703 Washers is likewise one of the excellent options for machining of nickel-primarily based totally superalloys because of their outstanding properties including excessive put on resistance, excessive hardness, and chemical inertness. They are observed able to withstanding excessive slicing speeds. But they have got decrease fracture longevity than carbide in addition to excessive velocity steel (HSS) inserts. Therefore, utilization of this Stainless Steel WNR 1.4438 Screws aren't counselled in excessive velocity machining of nickel-primarily based totally superalloys as they frequently come across unexpected failure because of speedy device put on, thermal-shocks, and decrease thermal conductivity. It turned into skilled that nano-coated gear supplied prolonged device existence than multi-layered micron-lined carbide inserts. Multi-coating factors had special friction coefficients that had been accountable for better intensity of microstructural deformation under the machined surface than uncoated insert.